US spends 10 trillion won to supply 500,000 chargers
From July, 55% of American parts must be used to receive subsidies.
Korean companies such as EVIS expand their factories
Self-development of core component ‘power module’
Korean companies are setting up production facilities in the United States one after another, targeting the electric vehicle charger subsidy policy in the United States, which will begin in earnest in July. At the same time, in order to meet the subsidy payment standards, efforts are being made to move away from Chinese products for ‘power modules’, a key charger component.
Oh Young-sik, CEO of EVSIS, an electric vehicle charger company under Lotte Group, said on the 7th, “We plan to establish an assembly plant and corporation in California, which has the largest number of electric vehicles in the United States.” “We plan to complete this by December.”
The reason that EVISYS chose July as the starting point for full-scale local production in the United States is related to the United States’ electric vehicle charger subsidy policy. This is because the electric vehicle charger subsidy policy introduced by the U.S. Joe Biden government in February of last year will be strengthened from July of this year. Parts worth more than 55% of the product cost must be manufactured in the United States to receive subsidies. As of the end of last month, 18 U.S. states had selected businesses eligible for subsidies. This year, the subsidy policy is expected to gain momentum as other states also begin selecting business operators.
The U.S. government’s goal is to invest 7.5 billion dollars (about 10 trillion won) to supply 500,000 chargers by 2030. This will open a large market in which the number of electric vehicle chargers in the United States, which currently number about 170,000, will triple within six years.
Accordingly, LG Electronics, which acquired Apple Mango, an electric vehicle charging company, in 2022, has been producing slow chargers in earnest at its factory in Texas, USA, since January of this year. They also plan to build a 350 kW (kilowatt) ultra-fast charger here in the second half of the year. Modern Tech, a charger specialist, also plans to start producing 600 kW chargers at its Texas plant in July through a joint venture with a local company in the United States.
Another company, Chaevi, signed a contract in October last year to supply 3,540 chargers to the North American market by 2025. Choi Young-hoon, CEO of Chaevi, said, “We are also thinking about outsourcing factories (in the U.S.),” and added, “Some companies are contacting us first, offering to lease factories.” Previously, among Korean electric vehicle charger companies, SK Signet had established a factory in Texas and sold products in the United States, but now a large number of companies have entered the U.S. market.
Domestic companies are trying to apply their own technology to ‘power modules’, a key component, in order to make more than 55% of the product cost from American parts. The power module, which converts alternating current into direct current, is a key component that accounts for 30-40% of the cost of an electric vehicle charger. Until now, cheap Chinese products have accounted for about 90% of the domestic power module market share.
In the case of SK Signet, it has currently set up power module production facilities at its Texas plant and is putting the finishing touches on local production in the second half of the year. EVIS aims to complete the development of its own power module product within the first half of this year (January to June).
Some companies are concerned that costs will rise significantly if they develop their own modules, so they plan to use power modules from Chinese companies produced in U.S. factories. An official from the company said, “Using power modules made by domestic outsourcing companies is 4 to 5 times more expensive than Chinese products, so profitability drops significantly.” He added, “I am worried that quality problems may occur in the early stages of development if charger companies produce them on their own, but in the end, “Having our own technology will also be something to consider in the future,” he said.
Source: Donga
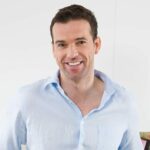
Mark Jones is a world traveler and journalist for News Rebeat. With a curious mind and a love of adventure, Mark brings a unique perspective to the latest global events and provides in-depth and thought-provoking coverage of the world at large.